SOMAG AG Jena Wins Prestigious Mittelstand Award
Jena-based SOMAG AG has been recognized as a 2023 recipient of the prestigious “Großer Preis des Mittelstandes” for its exceptional contributions to high-precision technology in aerial photography and data collection. Founded in 2004, SOMAG AG specializes in the development and manufacturing of Gyro Stabilization Mounts for various payloads, serving customers in over 50 countries.
The award ceremony, held on Saturday, 16th September 2023, saw company founder Konrad Steps receive the award, accompanied by former SOMAG engineer Bernhard Krauße at the award ceremony in Würzburg, Bavaria. SOMAG AG Jena congratulates Konrad Steps for his life’s work, highlighting his dedication and innovative spirit.
The company is also notable for its commitment to sustainability, innovative employee programs, and community support initiatives. This award highlights their significant impact on both the industry and the local community.
About the award: The Grand Prize of Medium-Sized Enterprises is a prestigious award in Germany that honors outstanding medium-sized companies. It is annually awarded by the Oskar Patzelt Foundation and recognizes exceptional achievements in areas such as innovation, commitment to the region, and job creation. The award promotes awareness of the economic and social significance of medium-sized businesses. Recipients are determined through a comprehensive selection process based on recommendations and submitted applications.
For more details, visit the official press release (in German).
Subscribe today!
Keep yourself informed about SOMAG and the latest Gyro Mount technology.
We will send you regular information about:
- exhibitions and event invitations
- new products, services and videos
- latest application examples, projects and partnerships
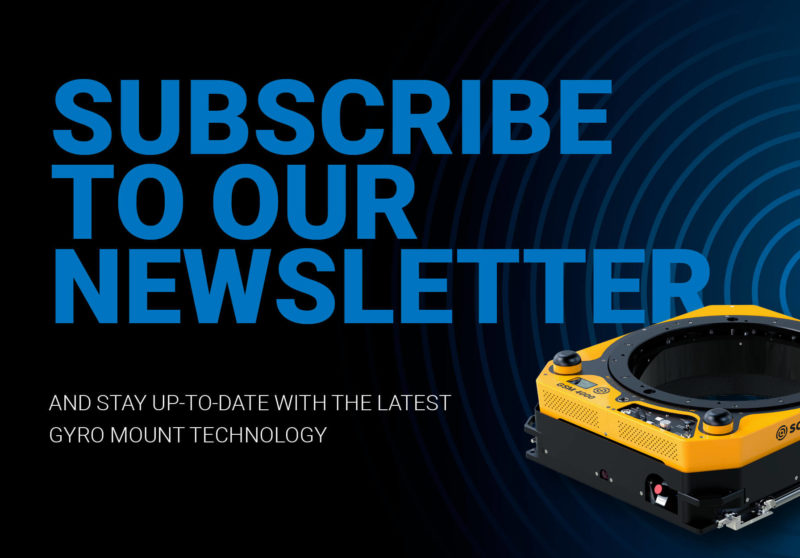